Scott Hoober’s family broke into the agribusiness world in 1941 when his grandfather, Charles ‘Bud’ Hoober, signed an agreement to sell International Harvester equipment in southeastern Pennsylvania. Hoober Inc. was born, and the family has been serving the mid-Atlantic region as a machinery and tools dealer ever since.
The Hoobers started exploring strip-till practices 15 years ago. They faced a big challenge right out of the gate, with heavy regulations in the northeast presenting a major obstacle.
“In Maryand and Delaware, they tell us what we can and can’t put on,” Hoober says. “We cannot apply certain levels of fertilizer in the fall. It must happen in the spring.”
Fall strip-tilling was completely off the table. On top of that, the practice was initially met with skepticism from growers in the region, Hoober says.
“Guidance was a huge issue early on,” he says. “There were challenges staying on the strip and we did not get the response we were looking for.
“Technology adoption was also a challenge for growers,” he adds. “Strip-till takes more management, investment and a willingness to make it work.”
Strip-Till Priorities
Hoober lists 5 priorities for a successful strip-till system in his region:
1. Maximizing yields and nutrient efficiency (more bushels per pound of fertilizer)2. Applying all three nutrients (NPK) together
3. Making strips in the spring (Md. and Del. regulations in the fall)
4. Preventing soil from drying out by keeping as much residue as possible
5. Minimizing runoff and having a positive impact on the Chesapeake Bay
The Hoobers committed to making it work in 2009 when they became the first dealer to put a Montag dry cart onto a Krause Gladiator unit. They were convinced dry fertilizer strip-till rigs were the way to go, until their first two customers told them otherwise.
“One customer switched rigs and the other quit strip-tilling all together,” Hoober says. “Neither felt like they were getting the most bang for their buck.”
Bucket Test Breakthrough
Hoober says he came to realize that fertilizer blends weren’t always consistent. Following his hunch that maybe dry fertilizer wasn’t the way to go after all, he devised a simple way to find out.
“We had a customer do a bucket test,” he says.
The customer planted corn in six buckets — three with dry fertilizer and three with liquid suspension fertilizer. It didn’t take long to see which worked better.
“You could really see the corn took up the liquid suspension fertilizer better in the early stages and filled out right through the end,” Hoober says. “That convinced us to go with suspension over dry right then and there.”
Liquid vs. Dry
It’s sometimes a struggle to get dry fertilizer converted fast enough for the plant to fully absorb in the spring, Hoober says.
“Dry fertilizer requires moisture. Often with dry fertilizer we’d get dry weather in June and couldn’t get the utilization out of it. Heavy suspension fertilizer doesn’t have to convert to a useable form. As soon as we get to that V3-V6 range, the suspension fertilizer is gone.”
“To get the most bang for our buck, we really have to use all three products (NPK) together…”
Hoober points out that clay needs to be added to liquid suspension fertilizer. It helps keep nutrients in the root zone towards the end of the growth stage. It’s also critical to have a trustworthy supplier.
“You need a really good potash when using suspensions or else it can become a hassle and create problems,” Hoober says. “We work with the Willard Ag fertilizer company. Their blending process really helped us improve our efficiency with suspension fertilizers.”
Closing the Corn Yield Gap
High yielding strip-till corn doesn’t happen by accident, Hoober says. While the highest corn yield ever was the 616 bushels per acre achieved by David Hula in 2019, most growers are harvesting much less; the average U.S. corn yield is 177 bushels per acre. The difference between the average yield and the potential represented by the record high is often referred to as the “yield gap.”
Hoober says proper nutrient uptake is key to closing that gap. And the key to uptake, he says, is getting the nutrients into the root zone. Using an application rate of 100 pounds of N and 40 pounds of P2O5 as an example, Hoober says nutrient concentrations in the root zone vary dramatically based on application method:
Broadcast & disced: 11 ppm N, 19 ppm P
Surface banded: 750 ppm N, 128 ppm P
Root Zone banded: 6,200 ppm N
(5-6 inches below seed) 1,200 ppm P
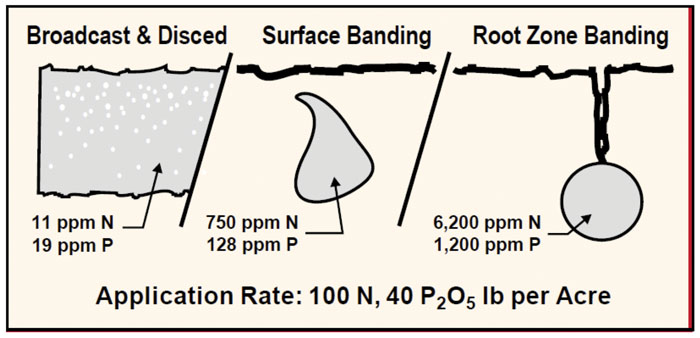
TIME TO CONCENTRATE. Nutrient concentration in the root zone varies greatly depending upon application method. With an application of 100 pounds of N and 40 pounds of P2O5, broadcast and disced dry fertilizer provided only 11 ppm of N and 19 ppm of P, compared to 750 ppm of N and 128 ppm of P with surface banding and 6,200 ppm of N and 1,200 ppm of P with zone banding.
Other factors in availability are timing and product type. Citing research from Pioneer, Hoober says 63% of N is used up through the tasseling stage, so it’s critical that it be in an available form during that timeframe.
“When we were using dry fertilizer, we couldn’t get it to convert fast enough for the plant to use it,” he says.
As an example, Hoober says a grower aiming for 300-plus-bushel corn, with a 36,000-plus population, might apply roughly 340 pounds per acre of nitrogen (N), 416 pounds of potash (K) and 157 pounds of phosphorus (P). In this situation, by day 12, N uptake is around 132 pounds, K is 183 pounds and P is 34 pounds.
“To get the most bang for our buck, we really have to use all three products (NPK) together. There’s no real advantage to deep banding N by itself because of the P and K elements being immobile. We want potash to go right to the roots. Banding the elements together in the strip really helps with the overall nutrient uptake.”
Hoober likens it to a buffet, saying crops like to “sit down and eat things together,” just like we do. He recommends applying fertilizer 5-6 inches below the seed, with seed depth generally being 1.75-2 inches in the mid-Atlantic region.
Overcoming Equipment Challenges
Hoober has faced a fair share of equipment challenges over the years, each one providing valuable teaching lessons on what’s needed to make a strip-till system work. Their first suspension fertilizer rig was a Case IH 5310 strip-till bar with a liquid tank on it.
“To be quite honest we didn’t have a lot of success with that bar,” Hoober says. “Shank depth was a big challenge. We really need each row unit to have its own depth control. Most of the units today have that, but the early ones did not.”
Learning from Mistakes
Hoober shares how one of his customers learned a valuable strip-till lesson last spring.
“He ran a strip-till rig when the ground was way too wet. He let it set, and it got dry in late April, early May. It was too rough when he stripped it. Then he tried to run the planter, and it had hydraulic down pressure. The DeltaForce was just all over the place. He ended up having to put it in manual because he couldn’t get it to settle down. He had a frustrating spring because of it. It all came back to the fact that he stripped way too wet, and it created big chunks, dried and got hard.”
Another issue they ran into was the inability to remove heavy residue from the strip without digging a trench. The early strip-till bars started out with a row cleaner in front, which wasn’t aggressive enough to move heavy residue.
“We needed that residue out of the way in order to make the strip as good as we could,” Hoober says. “Now with a lot of today’s machinery, the main coulter up in front splits the soil, there’s a wave that happens and that brings up the residue. Those discs will grab the residue and throw it out of the way very aggressively.”
Removing air pockets is also very important, Hoober learned early on. Air pockets will dry the soil out, ultimately creating problems with the planter and corn.
“You have to have some form of basket or roller,” Hoober says. “We actually hadone customer pull a packer behind his strip-till rig in order to get it packed down.”
Technology and equipment have come a long way in helping Hoober achieve his priorities consistently, but he says there’s still room for improvement.
“We’re still struggling with some of the same air pocket issues today,” he says. “We don’t have the strip as good as we would like to have it. I think we need more engineering or solutions to figure out how to eliminate some of those challenges we face.”